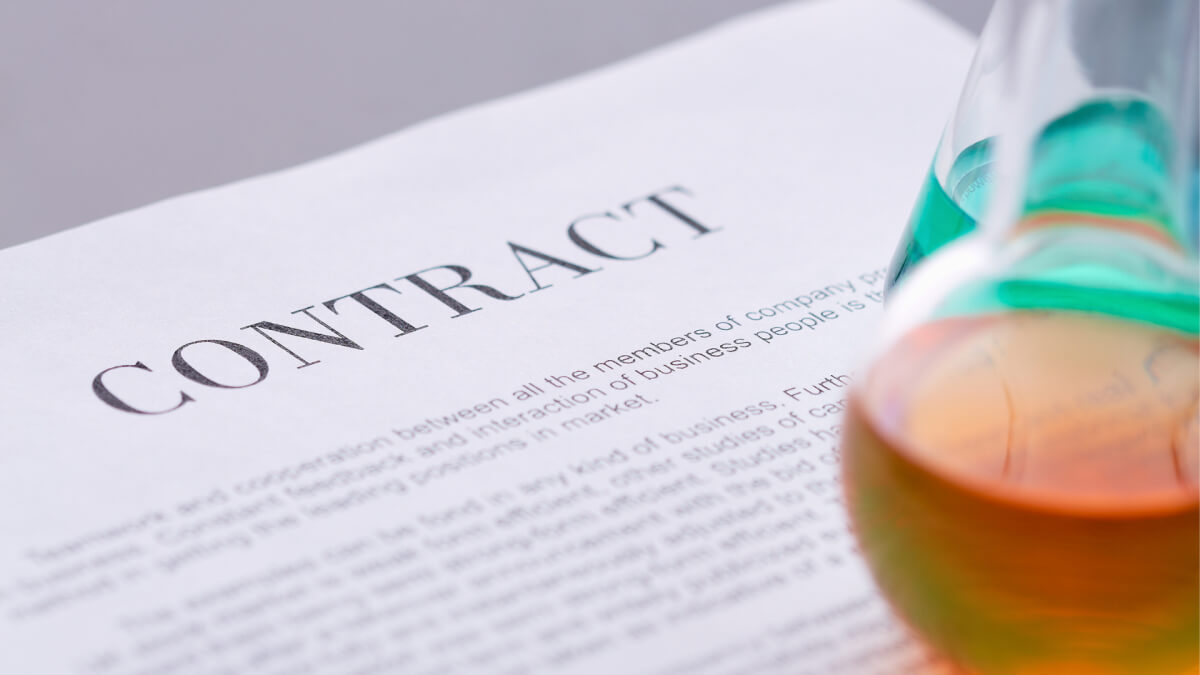
For busy academic and pharmaceutical research labs, it’s not easy to find time to manage multiple equipment contracts. Despite the importance of these contracts, it’s common that they unknowingly expire. This can cause a problem when maintenance is due on the equipment or if a repair is immediately needed, resulting in a higher than necessary risk of error, prolonged work stoppage, or worse, compromised safety. Therefore, it’s critical to have the right system in place to monitor these contracts, assess when maintenance is due, and manage when it should occur.
Managing a database of service contracts
When centralizing maintenance contracts, it is essential to utilize facility management software that can generate a user-friendly database, with the following information available to search and compare:
- Type of contract, including whether it’s an original equipment manufacturer (OEM) or multiple vendor repair (MVR) contract
- Equipment covered in the contract
- Types of maintenance/repairs covered in the contract
- Contract length
- Expiry date reminders
- Method of renewal
This is the first step to managing service contracts and coordinating all related activities. Without a user-friendly facility management system that can be integrated into a LIMS, these data are likely to be segregated and forgotten in the long term.
Integrating maintenance scheduling into basic workflow
Lab personnel are often focused on research-oriented tasks; experimentation is likely to take precedence over maintenance. With that in mind, integrating maintenance into the lab’s primary workflow will allow each member to plan around equipment maintenance periods. It’s advantageous to use a system dedicated to scheduling resource usage, especially for large departments, as most LIMS are not provided with the means to track all necessary service contract information nor are they capable of acting as hubs for lab equipment booking among many different labs in a given institution.
Many OEM contracts also provide low-cost training programs, so that they do not need to send their own technicians to fix the equipment every time a minor problem occurs. These can also be scheduled into the lab’s workflow, and personnel trained to use the lab equipment can be later identified in the facility management system, providing anyone who has an issue, regardless of the lab or department, the means to contact someone who is trained to fix the machine.
Tracking issues that occur can also be performed much faster using a dedicated resource scheduling software. This is especially important as without a means of tracking potential issues, any disturbances in the proper use of lab instruments are usually overlooked in lieu of finishing the technique or assay as quickly as possible. Because communication of these disturbances may be poor, the issue can be left unresolved until the machine finally breaks completely, either becoming a safety hazard or merely prolonging the amount of time necessary to begin using it again until a full repair is performed. Simply providing a system to mark these disturbances provides all personnel an opportunity to review the status of the equipment and judge accordingly whether maintenance needs to be performed earlier than anticipated.
Renew contracts faster
Renewing is often the part of managing maintenance contracts that is most commonly forgotten. Expiry dates are crucial to ensuring that lab equipment remains protected, and having a dedicated management system means that contracts can be renewed automatically, regardless of the vendor. This is crucial for high-value items, like mass spectrometers, flow cytometers, and chromatography systems, for which any slight perturbation can cause an extremely expensive repair. By unknowingly missing the renewal date, this type of error can inadvertently cost a lab a lot of money.
Centralizing service equipment contracts via dedicated software reduces the workload of lab managers and provides a system that reduces errors by tracking and managing the contracts in a single operational database. This type of system is also useful as a hub to reconfigure and renew contracts and foregoes the complexity of relying on separate spreadsheets and paperwork, especially for multiple instruments purchased from several different companies. Not only does it save time, but it helps safeguard all equipment throughout the lab and/or department, ensuring scientists can continually concentrate on their research instead of broken instrumentation.
Overall, the benefits of dedicated software include:
- Tracking all contracts, vendors, and equipment in a single, easy-to-access database
- Renewing and reconfiguring contracts quickly and effortlessly
- Safeguarding all major lab equipment
- Avoiding costly errors due to mismanagement of equipment repair and maintenance