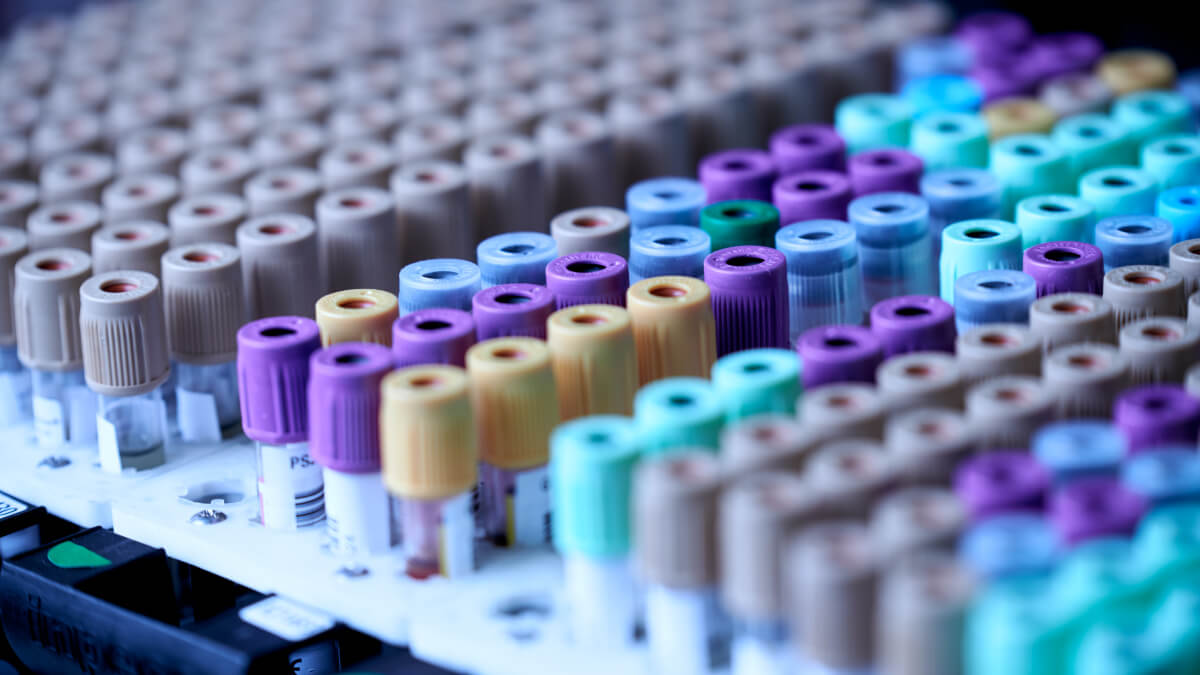
The modern-day R&D laboratory should be a place of creativity and collaboration where experts from different fields meet to share ideas, methods and successes. Yet highly trained scientists are often pulled away from their research to carry out manual administration tasks and attend tedious reporting meetings. Not only does this cause frustration for the scientist but it also decreases the operational capacity of the laboratory, introducing time and cost inefficiencies.
Disconnected data stifles discovery and collaboration
A key reason for operational inefficiency is the fact that data is often held in siloes. Paper notebooks, hard-drive-based documents and disconnected server-based software are common in the R&D laboratory. When each scientist or analyst works in a slightly different way, recording information in different formats and different locations, it can be very hard for teams to build on established findings and methods. This can lead to inefficiencies as scientists can’t easily learn from the successes and mistakes of the past and they waste time looking for information and creating established methods anew. Added to this, it’s almost impossible for team leaders to gain a complete understanding of the total work taking place in a laboratory at any one time or to take any learnings from this.
The struggle to adopt and integrate software
It’s clear that fragmented systems and data siloes are causing big issues in the laboratory but deciding to invest in software is a big decision. When existing systems don’t fully integrate with workflows or other software, users and other stakeholders might be resistant to add new systems. Added to this, the perception about the time and effort needed for data transfer, legacy system integration and training can be a barrier. In reality, integrating new software is often straightforward and requires little training, if the system is intuitive and meets all stakeholder needs.
Fragmented laboratory management
Manual methods of people, lab equipment and resource management are also having a big impact in the modern laboratory. Expensive equipment is often used by multiple teams and even outsourced to external companies and departments. Scientists need to know when equipment is available to design their workflow, but complex booking forms and complicated budget sign-off can lead to delays and bottlenecks. Similarly, laboratory managers need to know when equipment is sitting idle and when it could be rented out to maximize return on investment, without creating a pile of budget or invoicing paperwork. To ensure the reliability and reproducibility of results and compliance with regulatory standards, laboratory instruments must be regularly maintained and serviced. A reliable maintenance schedule must consider experiment workflows to minimize disruption in the lab while ensuring the validity of results. Again, this is difficult with manual and disparate systems.
Inventory management is also key to the modern R&D laboratory. The right resources must be available when and where they are needed. But, when systems are manual and there are multiple procurement procedures and personnel, it can be easy to run low on stock. Without the benefit of collective procurement, departments may miss out on the most reliable and cost-effective suppliers or the cost benefits that can be gained from buying in bulk. Together, these fragmented and manual methods of managing laboratory equipment can leave scientists frustrated, contribute to rising costs and lead to bottlenecks in critical workflows.